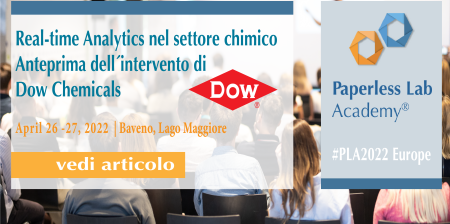
In previsione del suo intervento al Paperless Lab Academy® 2022, Lloyd Colegrove, director of data services e director for Dow’s Manufacturing and Engineering’s Industry 4.0 program ora in pensione, ha condiviso con gli organizzatori dell’evento, e loro con noi, alcune sue personali esperienze derivanti da 30 anni di impegno nel settore chimico.
Dopo 30 anni di lavoro nel settore R&D di Dow Chemicals, Lloyd decide di dare un cambio alla sua vita e si sposta nel dipartimento produzione.
In brevissimo tempo scopre una brutta verità: ingegneri e operatori non sapevano come gestire i dati o l’incertezza dei dati e per questo prendevano decisioni sbagliate nella gestione degli impianti. Inoltre, molti dei laboratori di qualità stavano cercando di spiegare ai dipartimenti operations che c’era un problema incombente, ma a causa di ciò che gli ingegneri e gli operatori guardavano nei loro schermi GPI, non credevano ai laboratori. Regnava una frustrazione generale. Mentre Lloyd svolgeva un lavoro quotidiano di supporto alla rete globale di laboratori di tutta l’azienda, attuando progetti di miglioramento e aiutando a risolvere i problemi dei singoli impianti in tutto il mondo, la comprensione dei dati e il modo in cui utilizzarli è diventato il suo interesse principale.
Prima di entrare nei dati in tempo reale, una delle prime cose che ha fatto è stata invitare un giovane collega a partecipare a un progetto. Era un ingegnere chimico con un dottorato in data science e aveva competenze davvero speciali.
Insieme hanno applicato, per la prima volta, un modello chemiometrico (oggi chiamato intelligenza artificiale, ma allora non conoscevamo il termine) a un sito produttivo che ha consentito un’analisi muti-variante dei dati di laboratorio. Questo progetto ha rivelato problemi casuali ma sistematici nella produzione dei lotti. Sebbene ci siano voluti due anni per risolvere il misterioso problema che esisteva da decenni ma che nessuno conosceva, abbiamo utilizzato il modello per evitare che i nostri clienti ricevessero determinati lotti di materiale che rientravano nelle specifiche secondo un approccio a singola variante (il modo normale di guardare i dati) ma era fuori dalla norma visto da una prospettiva multi-variante (qualcosa che nessuno aveva mai valutato prima nell’industria chimica).
Abbiamo pubblicato il primo articolo su questa applicazione nel 2007 che ha notevolmente aumentato la capacità del laboratorio di supportare la produzione, dando maggiore credibilità al processo di misura, che mancava di una dimostrazione analitica prima di questo progetto.
Una quantità enorme di dati: questo è il problema attuale dei laboratori
Il problema sono i dati, e troppi. Nessun essere umano può gestire tutti i dati generati da uno stabilimento. C’è un valore in tutti quei dati, ma gran parte di essi viene trascurato o semplicemente ignorato nella gestione a causa dell’enorme volume che si genera di minuto in minuto. Qual è l’unico momento in cui gli ingegneri possono esaminare un set di dati più ampio? Dopo che si è verificato un problema, che rallenta o arresta l’impianto! Allora, invece che capire il problema solo dopo che è avvenuto, attraverso l’analisi di dati, perché non provare a identificare il problema proprio mentre si sta verificando e affrontarlo in real-time? Ecco che parliamo di real-time analytics, e di prevenire e anticipare il problema (con l’IA, se possibile) e affrontarlo per tempo.
A tal fine, Lloyd ha collaborato con Northwest Analytics allo sviluppo della loro suite FOCUS Enterprise Manufacturing Intelligence: per la prima volta, gli impianti sono stati in grado di osservare un raggruppamento di dati molto più ampio e vedere – in tempo reale – come si comportavano i dati nell’impianto. Ciò ha portato a miglioramenti nel funzionamento dell’impianto quasi immediatamente e si è creato un chiaro valore: meno brutte sorprese, più occhi sui dati (esperti di tutto il mondo potevano osservare molto rapidamente il funzionamento di un impianto e fare una telefonata se vedevano qualcosa di preoccupante).
L’elenco continua. In uno degli stabilimenti da lui gestiti, il management ha avuto una brillante idea in fase di installazione del sistema FOCUS EMI: se puoi monitorare un impianto mentre è in funzione, perché non monitorare gli strumenti di laboratorio in tempo reale allo stesso modo? Un tecnico di laboratorio rientra da un fine settimana con amici e familiari e può, in pochi secondi, accertare lo stato di salute dei loro sistemi di misurazione e pianificare la giornata o la settimana. E, se lo desiderano, possono risolvere i problemi a casa dal loro smartphone, se necessario. Lo strumento viene utilizzato per tracciare e monitorare le calibrazioni e le misure di processo. Rende il laboratorio più efficiente e meno costoso da gestire.
Purtroppo l’intelligenza artificiale nel settore della chimica non si è evoluta tanto quanto avrebbe potuto.
La matematica dell’IA non è stata utilizzata per la risoluzione dei problemi, che avrebbero dovuto essere il passo successivo dopo la padronanza del controllo di processo.
L’implementazione dell’IA è una sfida. Per coloro che affermano che gli impianti chimici saranno gestiti dall’IA, Lloyd (e altri) dicono “non così in fretta”. Non esiste un set di dati sufficientemente completo a cui un algoritmo possa attingere per far funzionare un impianto senza il monitoraggio e l’intervento umano. Spetta alle persone imparare a usare l’IA per aiutarli a gestire gli impianti, non viceversa.
Dove invece il settore chimico ha subito un cambiamento radicale è invece la capacità di analisi in tempo reale, l’anticipazione e la pianificazione dei problemi che verranno, mosse molto più intelligenti e efficienti rispetto al dover eseguire un’autopsia su un impianto dopo che un problema ne ha causato il guasto.
Questa è una differenza fondamentale nella produzione chimica odierna. L’analisi in tempo reale aiuta i laboratori globali, gli ingegneri e gli operatori degli impianti a rafforzare la loro comprensione degli impianti e dei dati e ha aumentato la credibilità delle informazioni che escono dai laboratori. È una lotta: cambiare le abitudini e la prospettiva sulla visualizzazione e la manipolazione dei dati è molto difficile nella comunità di ingegneria e gestione degli impianti, ma il settore continua ad andare avanti in quest’area che ha un impatto positivo sulle persone, sull’ambiente e sui clienti.
Segui l’intervento di Lloyd Colegrove al Paperless Lab Academy® 2022 e
scopri il programma dei due giorni di conferenza